Special Report: Australian Vanadium’s test work on ore from its namesake project has produced high-quality vanadium flake comparable to products made by established peers.
Metallurgical test work to support the vanadium purification flowsheet for the Australian Vanadium Project in Western Australia successfully produced the 99.4 per cent purity vanadium pentoxide (V2O5) product.
Australian Vanadium (ASX:AVL) noted that both the ammonium metavanadate (AMV) and ammonium polyvanadate (APV) production routes were tested to allow optionality in the bankable feasibility study to simplify the refinery circuits and potentially lower both capital and operating costs.
Importantly, the work demonstrates the ability to produce high quality vanadium at scale.
“Test results have shown that the AVL process, using standard methods, has the capability to achieve high purity V2O5 throughout the life of mine,” managing director Vincent Algar said.
“This high purity product is comparable with the high purity vanadium products made by our established producer peers.
“This outcome comes from concentrating on thorough technical study work and using the process method improvements AVL has identified in that study work. Without doubt, this quality outcome further increases confidence in the project.”
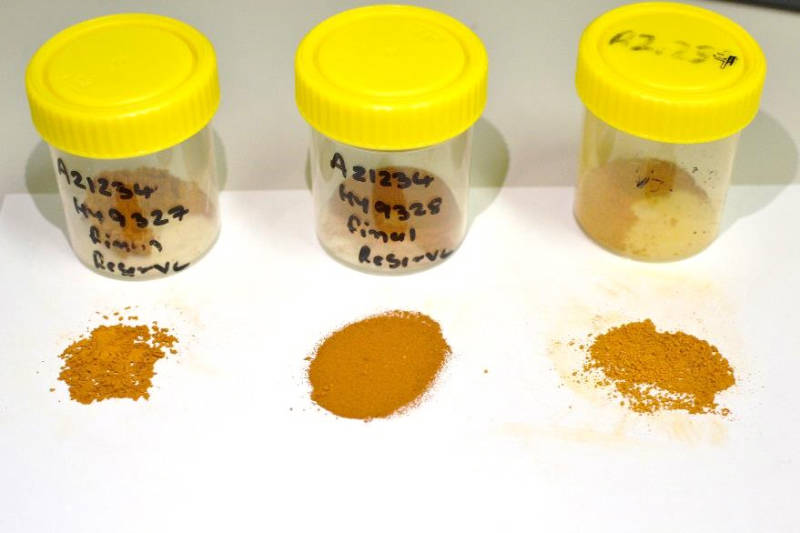
Vanadium test work
Metallurgical test work is underway to optimise the final stages of the vanadium refining process, which includes precipitation and V2O5 production.
All tests are performed on representative leach liquor derived from roasted concentrate material produced in pilot scale test work at Metso Outotec’s Dansville pyrometallurgical facility in the US.
The concentrate material was in turn produced from pilot scale crushing, milling, and beneficiation test work at ALS laboratories in Balcatta, Western Australia.
Standard refining used in producing V2O5 produces an intermediary chemical product called AMV that was the basis of Australian Vanadium’s pre-feasibility refinery flowsheet.
In parallel, the company also tested an alternative mature vanadium production route known as APV – a direction precipitation method that operates at lower temperature and lower pH.
The second process resulted in improved vanadium recovery, a reduced ammonium sulphate reagent consumption and the production of the top grade vanadium product.
Further APV optimisation work is currently underway to assess and determine the final purification flowsheet.
Once this refinery pilot test work is completed, larger samples will become available to evaluate further V2O5 purification, targeting products to service the vanadium redox flow battery and specialty chemical markets.
Bankable feasibility study
The metallurgical test work that will underpin the BFS processing flowsheets are nearing completion.
Significant pilot scale testing has been completed to validate an optimised concentrator flowsheet and a pelletisation and grate kiln roasting circuit for the front part of the refinery flowsheet.
Further leach and vanadium purification testwork is underway to optimise the downstream refinery flowsheet and this is forecast to be completed by the end of year.
Engineering consultant Wood Mining and Metals is updating the process design for the parts of the flowsheet that have been validated by pilot test work.
This will enable a progressive start of BFS engineering activities, which is targeted for completion in mid-2021.
This article was developed in collaboration with Australian Vanadium, a Stockhead advertiser at the time of publishing.
This article does not constitute financial product advice. You should consider obtaining independent advice before making any financial decisions.
www.stockhead.com.au