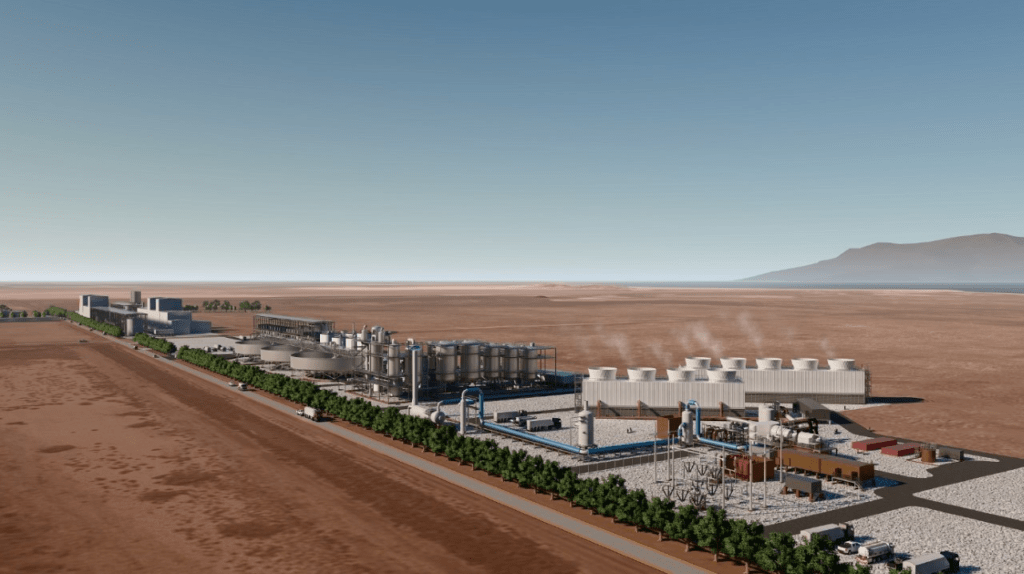
Decarbonisation through electrification and increased use of renewable energy are considered the biggest drivers of demand for lithium-ion batteries for grid storage and electric transport. However, from the supply-side, sustainability is a growing concern and area of interest for the clean energy sector.
LG Energy Solution recently signed a six-year lithium concentrate off-take contract with Sigma Lithium, with the supplier seeking to bring large volumes of what it called “green and sustainable” high purity lithium to the global market.
That deal signalled not only the importance of the energy storage industry being able to secure big quantities of materials over the long-term, but also the importance of ESG and transparency of supply chains, Shawn Shaw, energy storage director at Clean Energy Associates, told Energy-Storage.news at the time.
The European Union (EU) is seeking to introduce regulations on battery supply chain sustainability, while China — the world’s biggest battery making country at present — already has regulations on recycled content, as does South Korea.
Here are three more recent developments which may be relatively small steps, but the companies involved and the industry at large will be hoping they are indications of the types of solutions that can scale up for the mass market. Many other initiatives on sustainability exist of course, but hopefully these will be illustrative of the potential across the industry.
Construction begins at geothermal lithium extraction pilot in California
Energy-Storage.news reported in March 2020 that newly accessed geothermal resources in the Salton Sea area of southern California could also provide access to lithium extracted from geothermal brine.
Developer Controlled Thermal Resources (CTR) said on Monday that it has commenced drilling at the Hell’s Kitchen Lithium and Power project. The Salton Sea, a landlocked body of highly-saline water, already hosts about 450MW of geothermal power plants, but Hell’s Kitchen would be the first new one built in a decade.
“We are very pleased to kick start our drilling programme and we are on schedule to deliver the project’s first 50MW of baseload renewable power in late 2023 and an estimated 20,000 tonnes of lithium hydroxide in 2024,” CTR CEO Rod Colwell said.
After drilling to 8,000ft depth to create the power plant’s first two wells, the next step would be to test brine to prepare for scaling up the power plant’s generation output and lithium recovery potential, Colwell added. The extracted lithium will be converted into lithium hydroxide.
Investors in the pilot project include Bill Gates’s Breakthrough Energy Ventures, which put in US$20 million and the California Energy Commission (CEC) has described geothermal brine extraction as an opportunity to create a “world-class lithium industry” in the state. The CEC provided some financial assistance to the project.
The US government has said that developing domestic advanced battery supply chains is not only a matter of sustainability but also of international competitiveness and national security — the vast majority of materials and components even at the country’s handful of existing battery factories are imported from abroad, mainly from China.
Glencore, FREYR partner on ‘sustainable cobalt’
Undoubtedly the most-discussed material in lithium battery sustainability is cobalt. While increasingly, lithium iron phosphate (LFP) battery cells are being favoured for stationary energy storage and some electric vehicles (EVs), cell chemistries such as nickel manganese cobalt (NMC) have a huge market share in both industries.
Norway-headquartered battery manufacturing startup FREYR Battery has signed a contract for the supply of up to 1,500 metric tonnes of high grade cobalt metal cut cathodes with natural resources giant Glencore.
The cathodes will be sustainably sourced and made from partially recycled cobalt, which will be produced at Nikkelverk, a Glencore facility in Norway. FREYR is aiming to construct 43GWh of low carbon battery cell production facilities by 2025 and up to 83GWh by 2028 in Europe.
FREYR and Glencore will partner on reducing their carbon dioxide emissions, targeting carbon neutral materials production, while also collaborating on the introduction of recycling certificates to track the delivery of recycled material and processing of scrap.
As well as cobalt, a key component of FREYR’s battery cells, the pair are also looking into the supply of nickel and recycling of the NMC cells made at FREYR’s flagship battery factory in Mo I Rana, Norway.
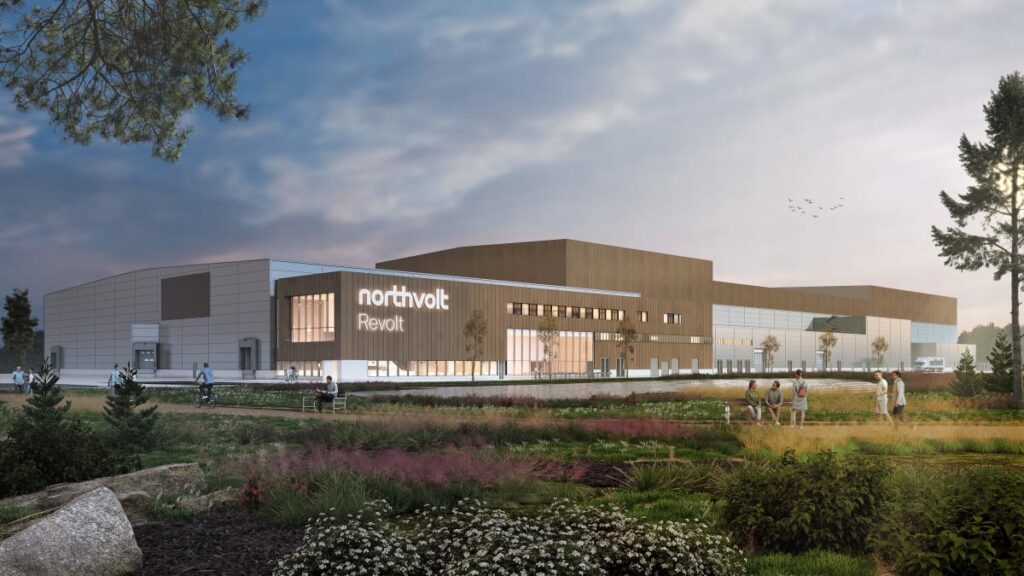
Northvolt makes recycled battery cells
Last week, another Scandinavia-headquartered battery manufacturing startup produced a battery cell using 100% recycled nickel, manganese and cobalt.
Northvolt, which is targeting 150GWh of annual lithium-ion battery cell production capacity in Europe, beginning with Northvolt Ett, a 60GWh plant in Skellefteå, Sweden. The company said that its recycling programme, called Revolt, will operate out of a facility adjacent to Northvolt Ett and could be scaled up to recycle 125,000 tonnes of batteries — equivalent to about 30GWh — per year.
Materials were processed from battery waste and the recycled cells made at Northvolt Labs, in Västerås, Sweden. The NMC cells demonstrated performance on par with battery cells produced from freshly-extracted metals, Northvolt said, after they underwent material validation and electrochemical performance testing.
Northvolt chief environmental officer Emma Nehrenheim said Revolt’s recycling process can recover as much as 95% of metals used in a battery to a high level of purity.
“What we have shown here is a clear pathway to closing the loop on batteries and that there exists a sustainable, environmentally-preferable alternative to conventional mining in order to source raw materials for battery production,” Nehrenheim said.
“What we need now is to scale-up recycling capacities in anticipation of future volumes of batteries requiring recycling.”
The Revolt plant will also recover copper, aluminium and plastics from batteries it processes. These will be recirculated back into manufacturing through locally-based third parties.
Construction at the large-scale recycling facility will begin in Q1 2022 and it will be operational in 2023, fed by end-of-life EV batteries and production scrap from Northvolt Ett. Northvolt is planning to supply batteries into the stationary energy storage space, as well as for EVs.
Another battery recycling plant is already being constructed with Northvolt investment in Norway. That plant will initially process about 8,000 tonnes of materials from EVs each year, and construction began towards the beginning of this year by Hydrovolt, a joint venture between Northvolt and Norwegian materials processing company Hydro.
At an online event hosted by the US Department of Energy earlier this year, JB Straubel, former Tesla CTO and now CEO of Nevada-based battery recycling startup Redwood Materials, noted that given the huge demand, recycled battery materials could compete on price with their newly-extracted counterparts.
www.energy-storage.news