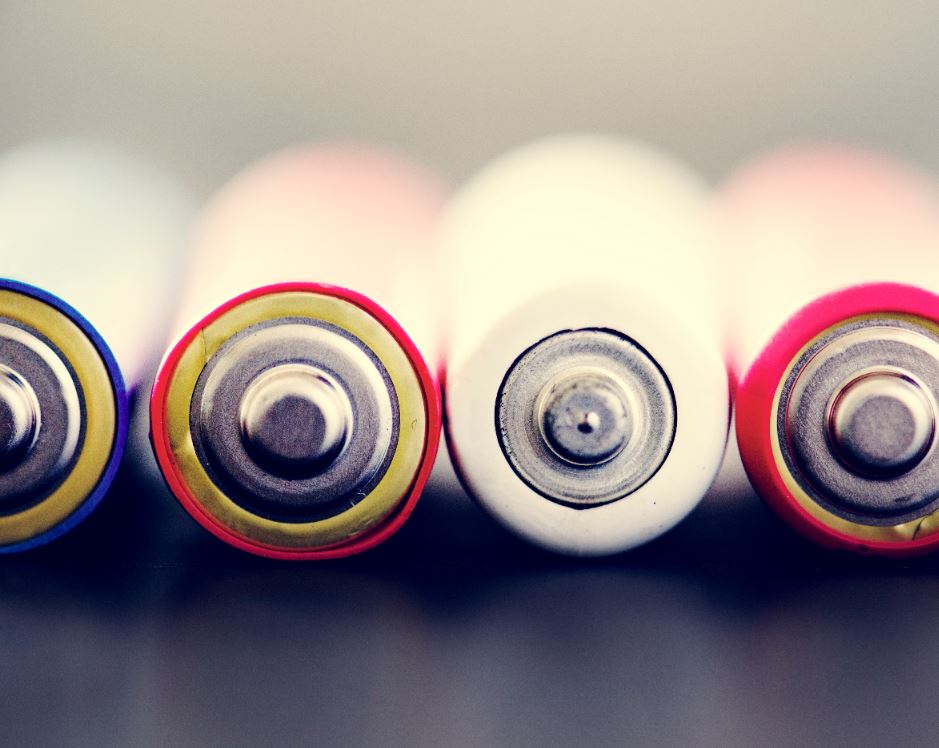
The growing push towards replacing traditional fossil fuel derived energy sources with renewables has seen increased attention on the so called “energy metals” i.e. those metals that are key to the future generation, storage and use of electrical energy.
Solar and wind energy are considered by many to be the panacea for all things fossil but it might not be so easy to continue rampant growth in these sectors. Both require specific exotic metals such as neodymium, indium and silver along with much rarer praseodymium and dysprosium in their manufacture and the demand may not be able to keep up with the supply.
According to a recent article in online Popular Mechanics magazine, by 2050 solar panels and wind turbines will require around 12 times as much indium as the entire world produces right now; neodymium production will have to grow by more than seven times, and silver will have to grow by nearly three times. And this is just for renewable energy; all of these metals have various uses in other industries.
If solar and wind alone cannot replace the world’s reliance on fossil fuels, then what about nuclear? Both nuclear and fossil-fuelled power stations use heat to produce steam that drives turbines and generators to generate electricity. But in a nuclear power station it is the fissioning of uranium atoms that replaces the burning of coal, oil, diesel or gas.
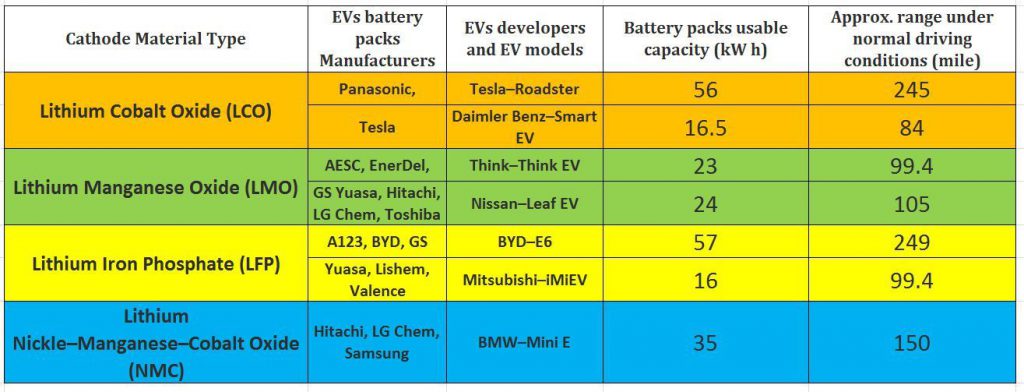
Nuclear plants can produce an enormous amount of energy with no carbon emissions – one tonne of uranium generates the same amount of energy as burning 130,000 tonnes of coal. Nuclear power can be generated consistently, where wind and solar are intermittent by nature. But according to the International Energy Agency (IEA), the share of nuclear power in the global energy mix has fallen from a peak of about 18% in the mid-1990s to 10% in 2018, largely due to concerns of radioactive waste and nuclear accidents like those that happened at Three Mile Island, Chernobyl and Fukushima.
Canada, however, has long been a leader in nuclear power. It currently makes up 15% of the country’s energy mix, and billions of dollars are being spent in Ontario to refurbish aging nuclear plants. But elsewhere, some large-scale and expensive conventional nuclear plants are aging out of commission. Canada is now positioning itself to be a leader in a new age of nuclear power by exploring the use of small modular reactors that generate under 300 megawatts of electricity. They would be cheaper and smaller than conventional nuclear power plants and are manufactured in factories. They are portable; they could be shipped to remote communities or job sites, such as the Alberta oil sands or mines that are off the grid and otherwise rely on diesel.

The demand for green power generation will be exacerbated as grid power is required to charge the batteries used in Electric Vehicles (EVs). The hype around EVs replacing combustion engine powered transport has been going on for some time but constrained by the development of reliable and efficient battery technology to provide the power. With advances in battery technology and with many jurisdictions around the world planning to legislate the banning of internal combustion engines in the future, the age of EVs may have finally arrived.
However, the continued transition won’t be easy. As well as the challenges in the grid generation, there are concerns over the future supply of many of the metals essential to the manufacture of EV batteries.
The lithium-ion battery is by far the dominant type. The structure of a typical battery cell has three primary functional components: a positive electrode, a negative electrode, and an electrolyte in between. The negative electrode (anode) is made from carbon usually in the form of graphite; the positive electrode (cathode) is a metal oxide, and the electrolyte is a lithium salt in an organic solvent.
Currently, graphite anodes are not manufactured in North America and further, there are only two operating graphite mines in North America – the Imerys Carbon and Graphite Mine in Quebec and Eagle Graphite Inc.’s [EGA-TSXV] Black Crystal Mine in BC.
EV manufacturer Tesla said recently that there could be a shortage of all of these key battery metals as a dearth of investment in mining has failed to keep up with the soaring demand. Lithium demand is set to more than triple through 2025, rising from 300,000 tons per year to over 1 million tons per year and the World Bank estimates that by 2050 demand for lithium, graphite and nickel will skyrocket by 965%, 383% and 108%, respectively.
Copper supply may also be affected as EVs need twice as much copper as conventional engines.
Tesla said recently that it might enter the mining business as it seeks to ensure that it can make enough batteries for future vehicles. Tesla is also trying to cut its use of cobalt that is primarily mined in the war-torn Democratic Republic of Congo where its production is associated with human rights abuses.
China controls about two-thirds of the world’s battery electric manufacturing capacity, a figure that is expected to rise to 73% by 2021, according to Bloomberg New Energy Finance (BNEF). By comparison, the US only accounts for about 13% of global lithium-ion battery manufacturing capacity.
An alternative to the lithium-ion battery is the nickel metal hydride battery, (NiMH). The chemical reaction at the positive electrode is similar to that of the nickel cadmium battery except that the negative electrodes use a hydrogen-absorbing alloy instead of cadmium.
Toyota has announced that the company will move its electrification goals forward by five years and remains the final frontier for the use of NiMH batteries in hybrid electric vehicles. Most other auto manufacturers committed to lithium-ion battery technology although Toyota has already shifted the hybrid drive-trains to be compatible with both battery technologies, for example in the 2018 Toyota Camry. Toyota’s rare earth NiMH batteries used in their HEV fleet have grown to account for over half of demand in 2018. Rare earths lanthanum and cerium are already significantly oversupplied, and batteries accounted for around 13% of demand for these elements in 2018, over 6% of which was in hybrid electric vehicles.
If Toyota switches battery technology away from NiMH, the demand for lanthanum (and to a lesser extent, cerium) will be adversely affected. An accelerated decline in demand for these elements in batteries would exacerbate the already expanding surplus supply as the rare earths industry focuses its attention on neodymium and praseodymium demand in magnets. Nickel supply concerns cathode manufacturers, as only a quarter of the nickel ore currently produced can meet the standards required for processing ore into nickel sulphate for cathode production in both NMC (Lithium Nickel Manganese Cobalt) and NiMH batteries. Cathode manufacturer BASF forecasts EVs to account for up to half of nickel demand by 2025.
The market share of the NMC cathodes was estimated by Macquarie Research to be around 23% of total EVs in 2015, but this share has increased over the last two years according to market participants. Many battery makers have switched to NMC batteries because of their lower cost and good capacity. In 10 years, as much as 80% of lithium-ion batteries will use NMC cathodes according to Cairn Energy Research.
To significantly reduce the quantity of nickel and cobalt in its cathodes, BASF aims to create ‘manganese-rich’ cathodes in the longer term. Roskill forecasts that manganese demand, just from lithium-ion batteries, will grow at a compounded annual rate of 23% from now until 2027.
The metal vanadium is used in the vanadium redox battery to store electrical energy on a large scale within an electrical grid. Electrical energy is stored during times when production (especially from intermittent power sources such as wind, solar and tidal) exceeds consumption, and returned to the grid when production falls below consumption.
As EV sales rise around the world, and the deployment of solar and wind also continues to scale up, Bloomberg noted recently that many of these clean technologies actually rely on the same supply chains and compete against one another for certain high-tech parts. As a result, some solar-component companies have to wait as long as 50 weeks for parts because EV companies are scaling up production, illustrating the bottlenecks that are beginning to appear.
But batteries can always be reconditioned, opening up opportunities in metal recycling perhaps somewhat offsetting the looming issues with supply.
www.resourceworld.com